Growing emphasis on increasing throughput by controlling process variation reflects an evolving understanding in industries as diverse as oil refining, pharmaceuticals, and food processing that it is possible to reduce costs and increase profits in the absence of significant investments in new process technologies. We have extended the steady state in widely varying settings using a methodology we call Robust Control, which focuses attention and problem-solving resources exclusively on process disruptions. It is a staged approach that involves simplifying a process, identifying and stabilizing the bottleneck, synchronizing the other stages with the bottleneck, and standardizing procedures to ensure that gains are maintained.
Large industrial systems have many parameters to be controlled and many levers for control. Individual controllers acting independently and without knowledge of one another can render a system noisy or even unstable. Increasing emphasis on controlling process variation by industries as diverse as oil refining, pharmaceuticals, and food processing reflects a growing understanding that reducing variation, because it increases throughput, has the potential to reduce costs and increase profits in the absence of significant investments in new process technologies.
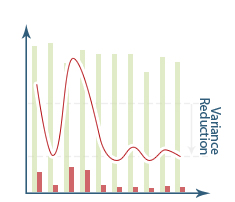
Dividing process variability by its mean yields the red line, which plots for actual plant data a threefold reduction in variance in a refining process subsequent to the implementation of Robust Control.
Consider the case of a glucose refinery plagued by highly variable output—standard deviation was on the order of 22%—despite operators routinely monitoring 2,000 input points and continuously adjusting some 40 controls. Reducing the input points to 40 and controls to 5 reduced variation by 75% and increased throughput by 15%, and subsequent implementations at five other refineries generated productivity gains on the order of 10%–50%. The aggregate capacity increase was valued at $300 million, equivalent to the cost of erecting a new refinery with a capacity of 1,000 tons per day. Additional savings in supplies and utilities were on the order of $3.5 million per year and finished goods inventory was reduced by more than 30%. Customers rewarded corresponding improvements in customer service with larger contracts over extended periods. And because existing processes can be run at higher capacity and with better precision under Robust Control, the company elected, in lieu of developing new, more expensive processes, to buy other companies’ plants and run their processes more efficiently.
A refiner of non-ferrous metals that implemented Robust Control achieved reductions of nearly 80% in the incidence of unknown disruptions and more than 70% in total disruptions over the course of a five-week experiment. Benchmarks made subsequent to expanding the implementation revealed reductions in disruptions in every critical process parameter. Aggregate gains from the implementation of Robust Control included a threefold reduction in process variability and concomitant improvement in the quality of output, a 25% capacity increase, and attendant savings in operations and maintenance.
The company not only maintained these gains, but deployed the same techniques in a host of other refining processes with equally dramatic results.
“Robust process control is transforming us into a learning organization. Every process problem is now viewed as an opportunity for learning and process improvement. We do not just gather data; we convert these data to valuable information for process analysis.”
—David Challenor, Cerestar N.V, Cargill Group
Breakthrough performance improvement is so seldom achieved because it almost always involves transforming vast stores of accumulated data into useful information—ultimately and ideally, into knowledge—and most companies lack robust systems and models capable of doing this. Robust Control is such a methodology. Experience has taught us to explore first opportunities for optimization because they are relatively straightforward to exploit and quick to deliver benefits. This is what Robust Control achieves through simplification. But the gains yielded by optimization should only whet a company’s appetite for the kinds of breakthrough improvements that are possible when firefighting is discouraged and problems with processes are solved once and for all, ends Robust Control pursues through root cause analysis.